The Definitive Guide to Alcast Company
Table of ContentsThe Best Strategy To Use For Alcast Company9 Easy Facts About Alcast Company ShownThe smart Trick of Alcast Company That Nobody is Talking AboutThe Greatest Guide To Alcast CompanyWhat Does Alcast Company Mean?Some Known Incorrect Statements About Alcast Company
Chemical Comparison of Cast Light weight aluminum Alloys Silicon advertises castability by lowering the alloy's melting temperature and enhancing fluidity during spreading. Additionally, silicon contributes to the alloy's stamina and wear resistance, making it important in applications where toughness is crucial, such as vehicle components and engine parts.It additionally improves the machinability of the alloy, making it much easier to process right into completed items. By doing this, iron adds to the overall workability of aluminum alloys. Copper increases electrical conductivity, making it helpful in electrical applications. It also enhances corrosion resistance and includes in the alloy's general strength.
Manganese contributes to the toughness of light weight aluminum alloys and improves workability. Magnesium is a light-weight component that offers toughness and influence resistance to aluminum alloys.
The Basic Principles Of Alcast Company
Zinc boosts the castability of aluminum alloys and helps manage the solidification process during casting. It enhances the alloy's strength and hardness.

The key thermal conductivity, tensile strength, return toughness, and prolongation vary. Amongst the above alloys, A356 has the greatest thermal conductivity, and A380 and ADC12 have the most affordable.
Excitement About Alcast Company
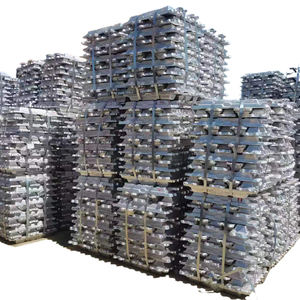
In accuracy casting, 6063 is fit for applications where intricate geometries and high-quality surface area coatings are critical. Examples consist of telecommunication rooms, where the alloy's premium formability permits smooth and aesthetically pleasing designs while maintaining structural stability. In the Illumination Solutions sector, precision-cast 6063 elements create elegant and effective lights components that call for complex shapes and great thermal performance.
The A360 shows premium prolongation, making it optimal for complex and thin-walled elements. In accuracy casting applications, A360 is well-suited for markets such as Customer Electronics, Telecommunication, and Power Devices.
Getting My Alcast Company To Work
Its distinct buildings make A360 a valuable selection for accuracy spreading in these find more info industries, improving product resilience and quality. Foundry. Aluminum alloy 380, or A380, is an extensively utilized spreading alloy with a number of distinctive characteristics.
In precision spreading, aluminum 413 radiates in the Consumer Electronic Devices and Power Equipment sectors. It's typically made use of to craft elaborate parts like mobile phone real estates, camera bodies, and power tool cases. Its accuracy is exceptional, with limited resistances as much as 0.01 mm, making sure perfect item setting up. This alloy's remarkable rust resistance makes it a superb selection for outside applications, guaranteeing lasting, sturdy items in the stated markets.
The Best Strategy To Use For Alcast Company
Once you have actually chosen that the light weight aluminum die casting procedure is suitable for your task, a vital following action is picking the most appropriate alloy. The light weight aluminum alloy you pick will substantially influence both the casting process and the residential or commercial properties of the last product. Due to the fact that of this, you must make your decision very carefully and take an informed method.
Establishing one of the most ideal aluminum alloy for your application will indicate evaluating a vast array of attributes. These relative alloy attributes adhere to the North American Die Spreading Organization's standards, and we have actually divided them into two classifications. The very first group addresses alloy features that influence the production process. The 2nd covers attributes influencing the residential or commercial properties of the last item.
Getting My Alcast Company To Work
The alloy you select for die casting directly influences a number of facets of the spreading process, like just how simple the alloy is to work with and if it is prone to casting flaws. Hot cracking, likewise called solidification breaking, is a regular die spreading problem for light weight aluminum alloys that can cause internal or surface-level splits or cracks.
Specific aluminum alloys are much more vulnerable to warm splitting than others, and your option must consider this. One more usual problem located in the die casting of light weight aluminum is pass away soldering, which is when the cast stays with the die wall surfaces and makes ejection difficult. It can harm both the actors and the die, so you need to seek alloys with high anti-soldering homes.
Rust resistance, which is already a noteworthy quality of aluminum, can differ considerably from alloy to alloy and is an important characteristic to take into consideration depending upon the environmental conditions your item will be revealed to (Casting Foundry). Use resistance is another property generally looked for in light weight aluminum items and can set apart some alloys